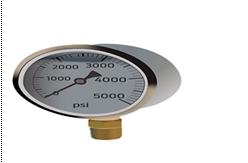
How to Save Time and Expenditure by Choosing a High Quality Pressure Gauge
A pressure-powered machine can use a pressure gauge to measure the intensity of fluid, gas, water, or steam to ensure no leaks or pressure variations could ruin the system’s function. Techniques for managing pressure are fashioned to function within a specific pressure range. Any departure from the tolerable standards significantly affects how the system performs. Pressure gauges are examined in-depth in this article.
Pressure gauges regularly check Pipeline pressure, ensuring that gases, liquids, and steam are transported safely. Pressure gauges assess the functioning of pumps, conveying systems, and different kinds of spray nozzles.
The primary functions of pressure gauges are to inform users of a system’s status and guard against leaks and equipment damage.
Some features that affect pressure gauge price in Kenya are listed below;
Accuracy
The role of the pressure gauge, which can be anything from simple testing to monitoring intricate industrial processes, determines the needed precision. On the full scale, testing pressure gauge accuracy should typically range from the percentage of 0.25 to 0.10, whereas essential procedures require an accuracy percentage of 0.5. An accuracy of 2% is possible for less critical processes.
Dial
The sizes of pressure gauge dials, which range from 1.5 inches to 16 inches, are as diverse as the different pressure gauge kinds. The dial will be located, and the level of accuracy needed will determine its size.
The Display
Analogue screens have long been the primary and most widely used option. The selection of screens has changed recently as digital displays have proven to be adequate. The type of application is the final determining element of the kind of display.
Environmental Factors
Environmental elements significantly influence any monitoring, and the temperature is a significant one that has a big impact on pressure gauge readings. Models of pressure gauges exist that take temperature into account. The indicator should be segregated for protection in areas with large temperature swings. One should utilize the weatherproof and sealed fluid-filled pressure gauge in situations containing corrosive substances, particle matter, or wet and humid circumstances.
The Media to Be Monitored
The pressure gauge chosen should be compatible with the material that will be monitored and tested. Stainless steel gauges offer excellent protection from shocks, vibrations, and temperature extremes and are a popular choice for corrosive environments like wastewater treatment facilities, petrochemical processing, or chemical production.
Connections
When selecting the connection, one should consider the process pressure, gauge size and weight, space requirements, and leak integrity.
Various Pressures
Maximum operating pressure of no more than 75% of the whole scale range is commended. Choosing a pressure gauge outside this range may lead to wear and failure of the indicator.
What the Pressure Gauge Costs
One must prioritize this when choosing a pressure gauge, among other things, since one must stay within their budget despite all other factors. Seek out retailers that offer specialized, personalized discounts and promotions.
Conclusion
Pressure gauges are a vital tool used by industry to gauge the pressure in a system as a quality control measure and to guarantee product consistency. To prevent premature gauge failure, gauge accessories, such as specialized restrictors, or even diaphragm seals, may be required depending on the application requirements.