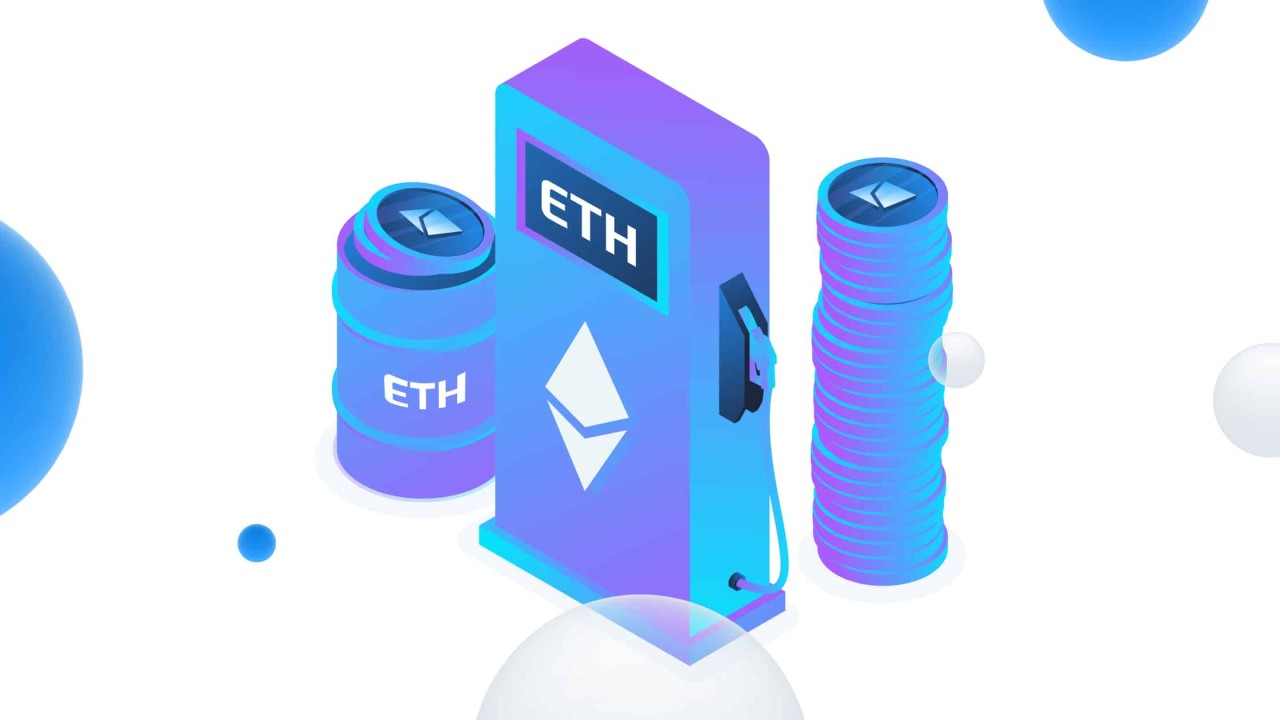
Unlock Cost Savings: Optimize Usage with our Efficient Gas Cylinder Sizes!
Maximizing Gas Cylinder Usage
One of the best ways to maximize gas cylinder usage is by choosing the appropriate size for your specific needs. It’s essential to understand that different cylinders have varying capacities, and using a larger cylinder than is necessary can lead to wastage. Therefore, it’s crucial to estimate your gas consumption requirements accurately and choose a cylinder size that meets those needs.
Another way of maximizing gas cylinder usage is by implementing safe handling practices. Gas cylinders should always be handled with care as they contain compressed gases under high pressure. Proper storage, transportation, and usage practices can help minimize leakage and ensure you get the most out of each cylinder. Additionally, investing in quality regulators and valves can help you control gas flow more efficiently and prevent leaks or accidents.
Finally, monitoring your gas usage regularly can also help maximize its efficient use. Keeping track of when cylinders were last refilled or replaced can ensure you avoid running out mid-project or wasting unused contents due to outdated expiration dates. By following these tips, businesses can optimize their gas consumption while reducing costs and minimizing environmental impact at the same time!
Here is a gas cylinder size chart that provides information on common gas cylinder sizes:
Size: 9 kg
Dimensions (Approx.): Height – 580 mm, Diameter – 310 mm
Typical Applications: Residential cooking, small appliances
Size: 14 kg
Dimensions (Approx.): Height – 700 mm, Diameter – 310 mm
Typical Applications: Residential cooking, small appliances, outdoor grilling
Size: 19 kg
Dimensions (Approx.): Height – 845 mm, Diameter – 310 mm
Typical Applications: Residential cooking, small appliances, heating
Size: 45 kg
Dimensions (Approx.): Height – 1250 mm, Diameter – 375 mm
Typical Applications: Commercial cooking, industrial use, heating
Size: 50 kg
Dimensions (Approx.): Height – 1330 mm, Diameter – 375 mm
Typical Applications: Commercial cooking, industrial use, heating
Please note that the dimensions and applications mentioned above are approximate and may vary depending on the specific brand and model of the gas cylinder. It’s always advisable to consult the manufacturer or gas supplier for accurate and up-to-date information regarding gas cylinder sizes.
Benefits of Optimizing Gas Cylinder Usage
Optimizing gas cylinder usage can bring several benefits to both businesses and individuals. One of the most significant advantages is cost savings. By using appropriate cylinder sizes and reducing unnecessary wastage, users can minimize their expenses related to gas procurement, handling, and disposal.
Besides saving costs, optimizing cylinder usage also helps in improving safety standards. Proper storage, transportation, and handling of cylinders reduce the risks of accidents or incidents that might occur due to mishandling or inadequate storage facilities.
Another benefit associated with optimized gas cylinder usage is environmental sustainability. The efficient use of gases reduces emissions by minimizing waste and conserving resources. This makes a positive impact on the environment while promoting greener practices in day-to-day operations. In summary, optimizing gas cylinder usage brings financial benefits along with safety improvements and environmental sustainability.
Tips on How to Optimize
Optimizing the usage of gas cylinders is crucial for cost savings. Here are some tips on how to optimize their usage:
- Plan ahead: Knowing your gas requirements in advance can help you choose the appropriate cylinder size and avoid unnecessary expenses.
- Proper storage: Store cylinders in a cool, dry, and well-ventilated area to avoid contamination and deterioration.
- Regular maintenance: Keep the cylinders clean and conduct regular inspections to ensure they are functioning efficiently and safely.
- Use the right equipment: Using compatible regulators, hoses, and other fittings ensures that you get maximum performance from your gas cylinder.
- Proper handling: Handle cylinders with care, following safety guidelines when moving or transporting them.
By following these simple tips, you can optimize your gas cylinder usage while reducing costs without compromising on quality or performance.
Case Studies: Real-Life Examples
Case studies are a valuable resource for businesses and organizations looking to make informed decisions about their operations. They provide real-life examples of how others have tackled similar challenges, offering insights into what works and what doesn’t. In the context of optimizing gas cylinder sizes for cost savings, case studies can be particularly useful.
For example, one case study might examine how a manufacturing plant replaced its existing gas cylinders with smaller, more efficient models. By doing so, they were able to reduce waste and optimize usage, resulting in significant cost savings over time. Another case study might focus on a laboratory that switched to larger gas cylinders in order to meet increased demand without sacrificing efficiency or safety.
Overall, these case studies serve as concrete examples of how optimizing gas cylinder sizes can lead to tangible benefits for businesses and organizations of all kinds. Whether you’re looking to reduce costs, improve efficiency, or enhance safety measures at your facility, taking cues from successful real-life examples is an excellent way to get started.
Conclusion: Unlocking Cost Savings
Shining, a leading manufacturer of gas cylinders, has been able to unlock significant cost savings by implementing innovative strategies. The company realized that its traditional production methods were not efficient enough to keep up with the demands of the market and decided to explore new ways of manufacturing. By investing in technology and automation, Shining was able to reduce its operating costs significantly.
One of the key changes made by Shining was the implementation of an automated production line for its gas cylinders. This allowed for faster and more accurate manufacturing, reducing the number of mistakes made during production. Additionally, automation helped to reduce labor costs as fewer human workers were needed on the factory floor. Overall, this change resulted in significant cost savings for Shining while also improving productivity levels.
Another strategy employed by Shining was the use of predictive maintenance techniques on their equipment.