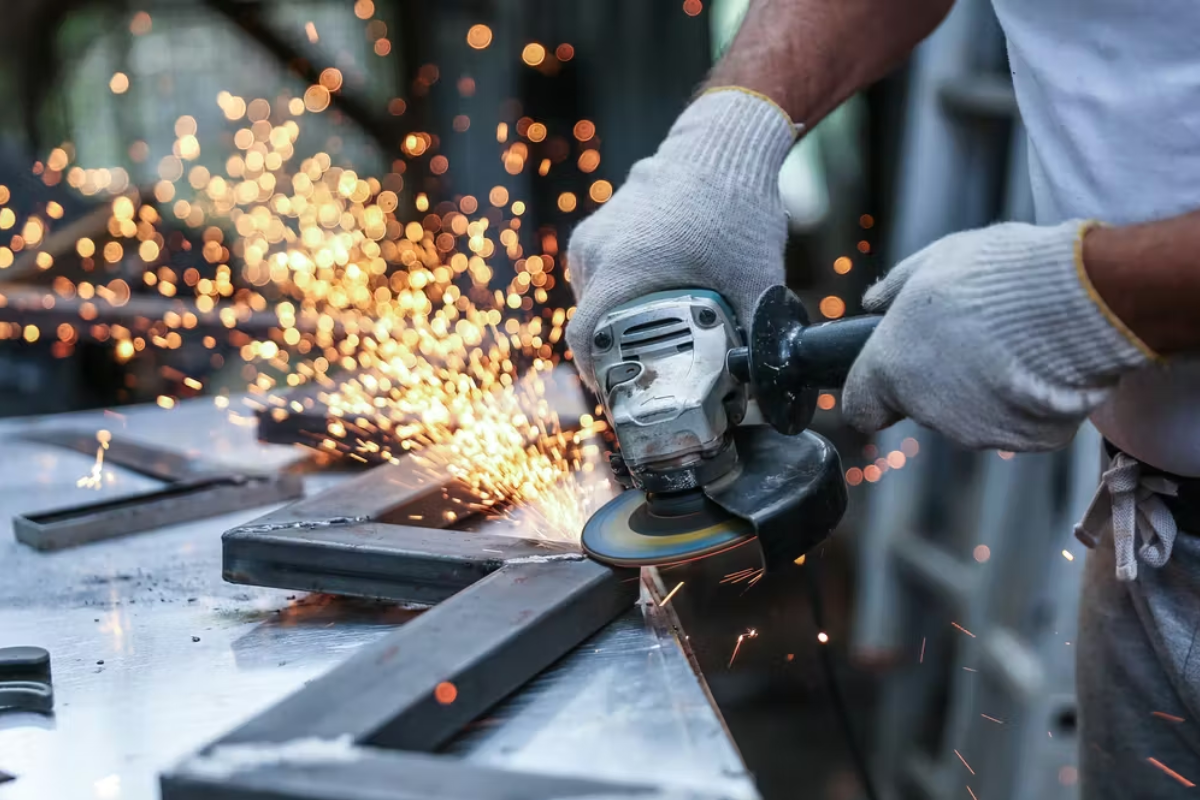
How Grinding Optimizes Material Hardness and Wear Resistance
Introduction
The impact of grinding techniques on the resulting surface hardness and wear resistance material properties has been prominently adopted across a range of industries where superior hardness and wear resistance characteristics are a requirement. Whether in construction, automotive manufacturing, or metal fabrication, a grinding process provides an in-demand approach to molding and hardening materials as well as augment their resistance to wear and tear. A key element of this operation is the grinding disc (UDO ผู้จัดจำหน่ายใบเจียร), which not only perfects surfaces but also enhances material properties. In this article, we’ll look at how different grinding processes can improve the durability of a material and why selecting the optimal grinding disc is crucial to make these results achievable.
Material Hardness and the Science Behind Grinding
Grinding is a machining process that uses an abrasive wheel or other abrasive media to remove material, creating a smooth, polished, or hardened surface. This method enhances a material’s hardness by compacting its outer layers, which results in denser molecular structures that are better able to resist impact, friction and deformation.
A major player in this change is the friction created by the grinding disc, which heats up and compresses the surface of the material. Used correctly, this process improves the microstructure of metals and other materials, making them significantly harder and more wear-resistant. Grinding extends the lifespan of parts, minimizes maintenance requirements and enhances the reliability of products across industries including aerospace, automotive and construction.
As an example, during steel fabrication, grinding can be used to increase hardness by creating a harder case on the surface. The resulting hardened outer shell can help to repel both abrasion and corrosion, rendering the material well-suited for use in challenging environments. Without grinding discs and the precision they afford, achieving this level of durability on a shoe would be challenging, if not impossible.
Grind Layers to Increase Wear Resistance
Grinding not only increases hardness, but also wear ~ a vital characteristic of material subject to repetitive motion and extreme environments. Wear resistance is the ability of a material to withstand corrosion, friction, and general degradation over time. Here, the grinding disc plays an influential role because it enables the technicians to control how much material has to be removed ensuring that the surface is functional and maintains its strength.
In applications like industrial equipment, machinery parts, and cutting tools wear-resistant materials are widely used. These parts can suffer significant wear from high-pressure operation and thus need surfaces that don’t degrade readily. With appropriate grinding techniques, manufacturers can produce high performance, resilient, and near nett parts, which result in less downtime and more efficient production lines.
In addition, grinding is fundamental in producing protective coatings on materials. Carbide-coated surfaces are often less effective until after they have been ground. Specialized grinding discs achieve the surface smoothness and thickness required to proceed with applying the family of defensive coatings.
How To Choose The Best Grinding Disc For Maximum Efficiency
All grinding discs are not created equal, and the way you pick can have a major impact on the end result of a venture. Which of these discs is ideal for the job depends on the material type, grinding speed, and required surface finish. For example:
- Aluminium oxide discs: are most reliable when grinding steel, and other hard metals, and they are very durable.
- Silicon carbide discs: are ideal for use on non-ferrous materials such as aluminum or brass.
- Diamond discs: used for precision with work projects requiring fine finishing or ultra-hard carrying materials, including glass and ceramics.
Using the right grinding disc will allow operators to maximize material removal while minimizing tool wear. This leads to uniform surface finishes, increased hardness, and highest wear resistance.
Enjoying the Most Flavor with Proper Grinding Techniques
Professionals must use a method that balances speed, pressure, and cooling to maximize the impact of grinding. Too much pressure causes overheating, which can result in surface cracking and reduced wear resistance. Conversely, if not enough grinding pressure is applied, the material may have a soft or rough surface. This ensures the grinding disc can effectively perform its purpose while maintaining the integrity of the workpiece.
Using coolants or lubricants in grinding processes also keeps it at a constant temperature and prevents thermal damage. Technicians can achieve maximum hardness and wear resistance if best practices are followed, creating components with optimal performance and longevity.
Conclusion
We cannot stress enough how critical grinding is to the process that increases the hardness and resistance to wear in materials. Using the right techniques and tools — and especially the ideal grinding disc — manufacturers can create lasting, dependable materials for use in countless industrial processes. Grinding is an essential process in any industry that prioritizes performance and longevity — from extending the life of machinery components to enhancing the general quality of products used in manufacturing.